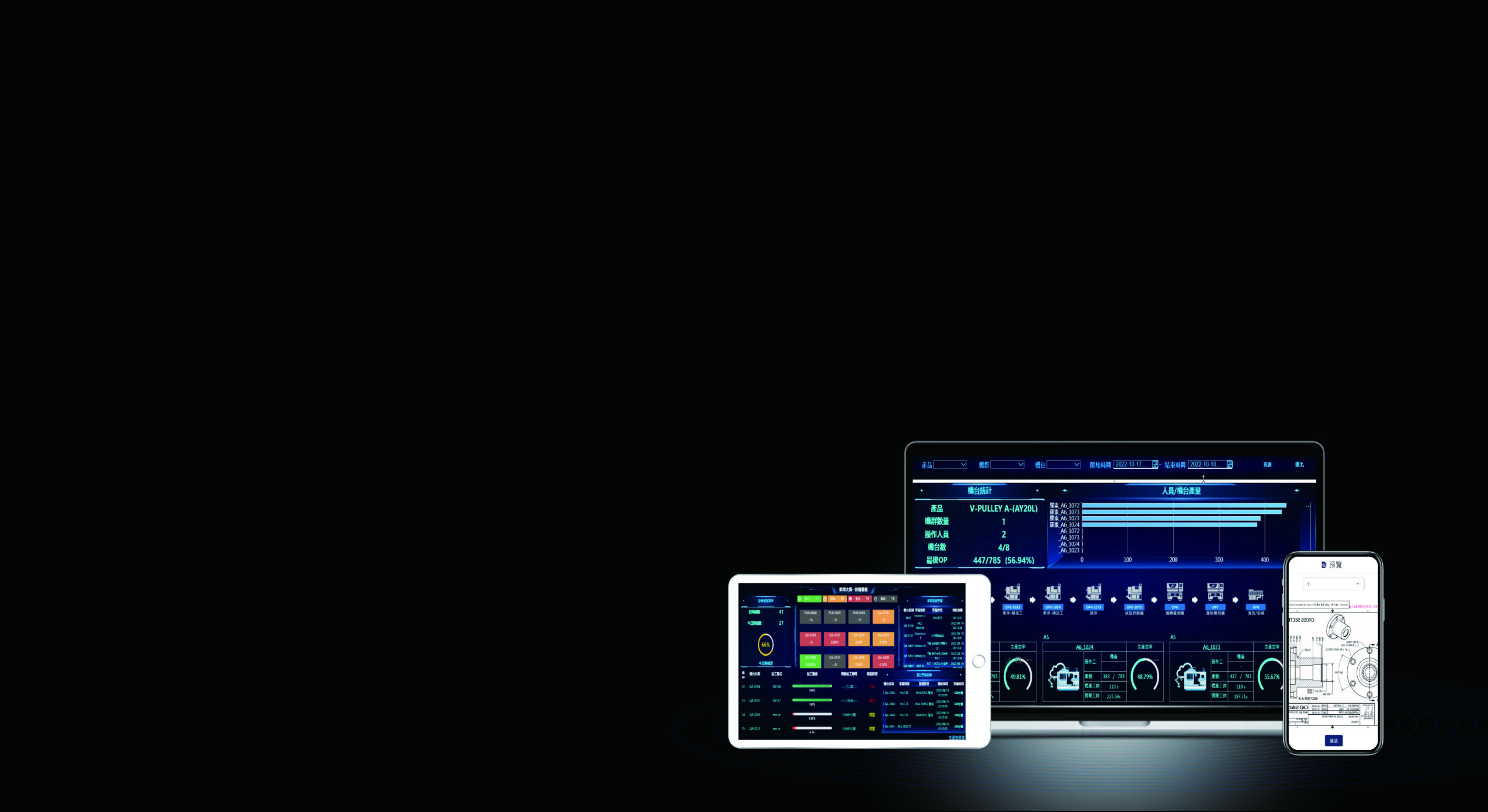
Synfactory
SynFactory Smart Production Cloud leverages equipment data to drive lean factory management,
acting as the ‘doctor’ of the factory to address and resolve production management challenges
SynFactory is a system that manages the entire manufacturing process and drives production optimization, acting as the central hub for vertical integration in smart manufacturing. It interfaces with upper-level systems such as ERP, PLM, and WMS for planning management and connects directly to production equipment. It integrates data from various systems, issuing control commands to the equipment based on real-time conditions, while also uploading equipment status and data to the management level. SynFactory is an indispensable part of the smart manufacturing ecosystem.
As a factory manager, do you face any of the following challenges?
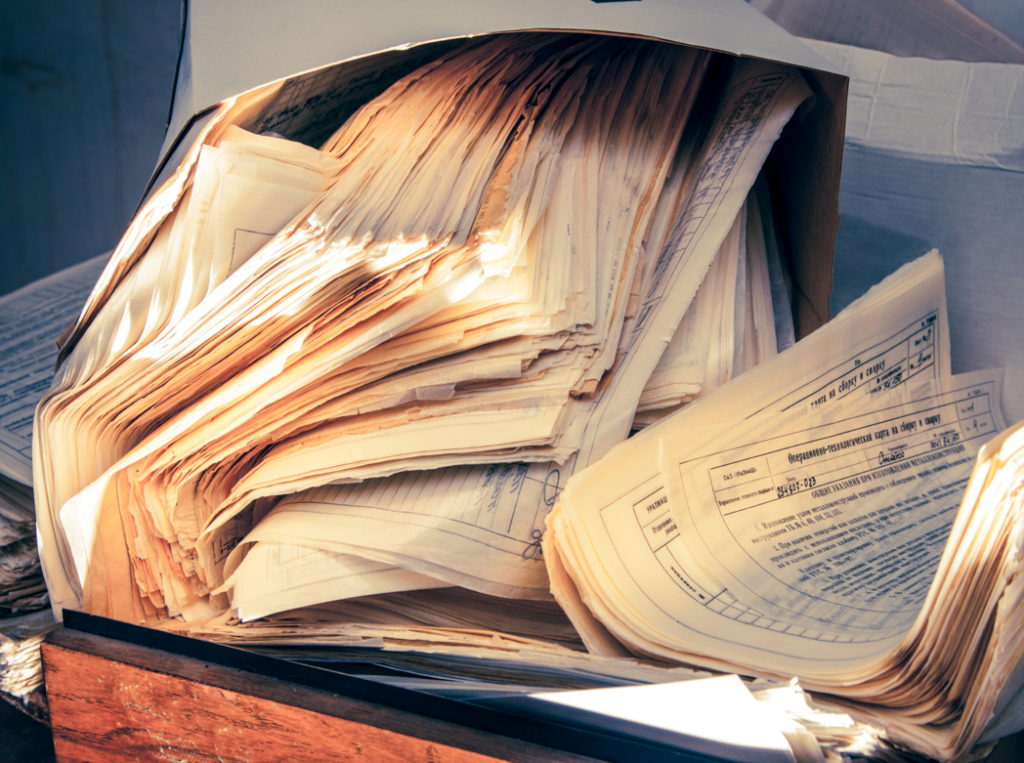
Paper drawings are hard to maintain
Paper drawings are easily damaged, and frequent reprints waste resources. Moreover, managing paper files and versions control is challenging, resulting in disorganized and difficult product process documentation.
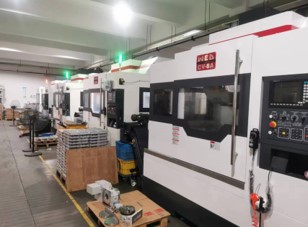
Obtaining equipment information
is challenging
Difficult to accurately track the utilization rate of each machine, and the significant disparity in capacity usage across stations leads to reduced overall equipment efficiency or excess work-in-progress inventory at the production line.
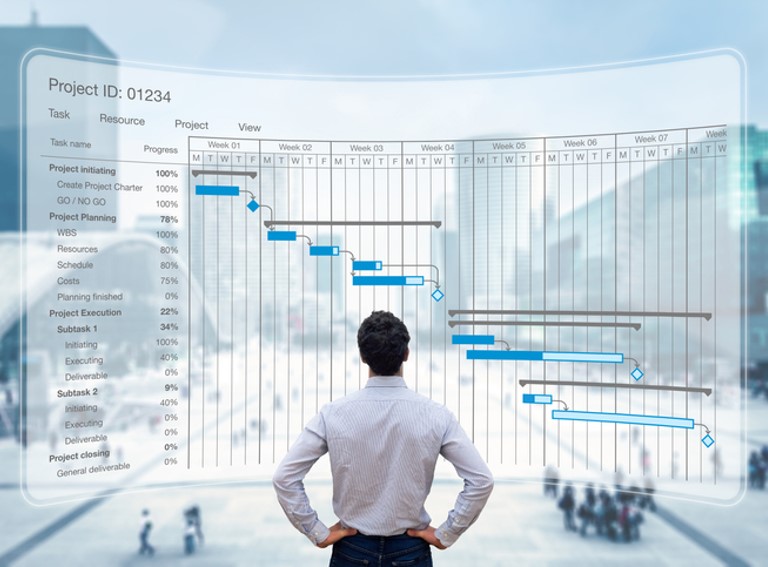
Tracking production progress
is challenging
Manual reporting often causes delays, making it hard to monitor real-time progress accurately, which leads to issues with production scheduling and order management.
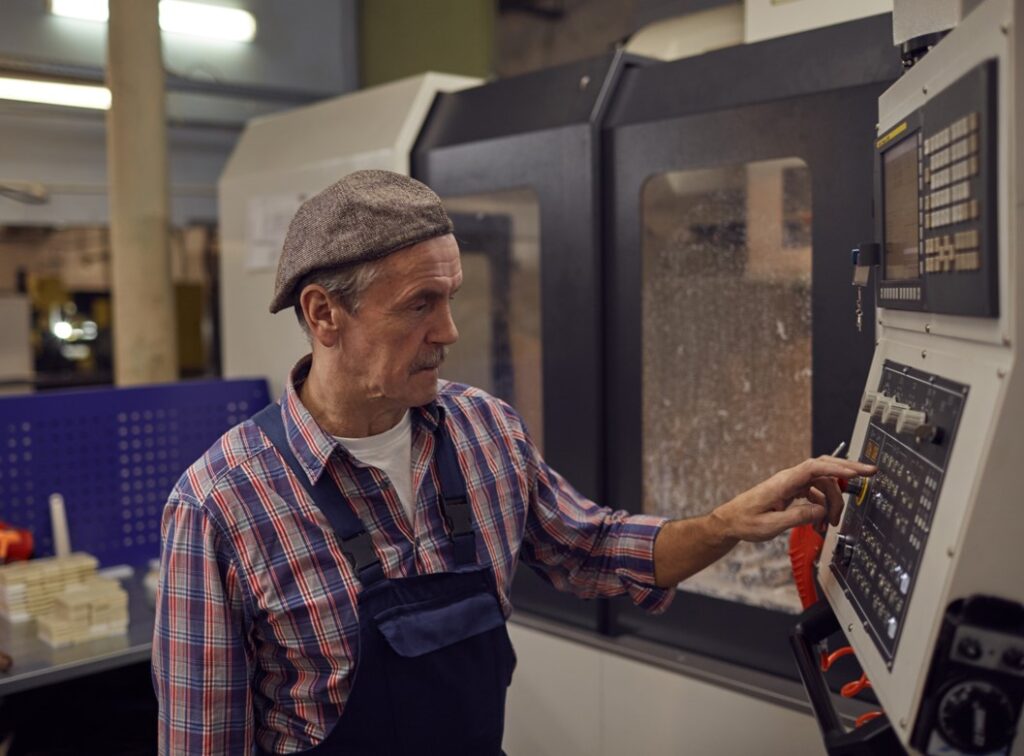
Technical knowledge preservation
is challenging
Experience is gained over time, without standardized SOPs, and relies largely on subjective judgment, making it challenging to transfer knowledge and skills.
Core Strength
Leveraging machine network as the core foundation, the factory management system platform integrates multiple functional modules into a single solution.
Its architecture encompasses the equipment layer, data collection layer, and application layer, fully designed to meet the diverse management needs of the factory.
Simple and User-friendly
Simple and user-friendly. The system features an intuitive interface and streamlined workflow design tailored to different usage scenarios. It supports multi-device applications, including computers and mobile devices such as smartphones and tablets. Manage your factory easily from anywhere, anytime, with just one device.
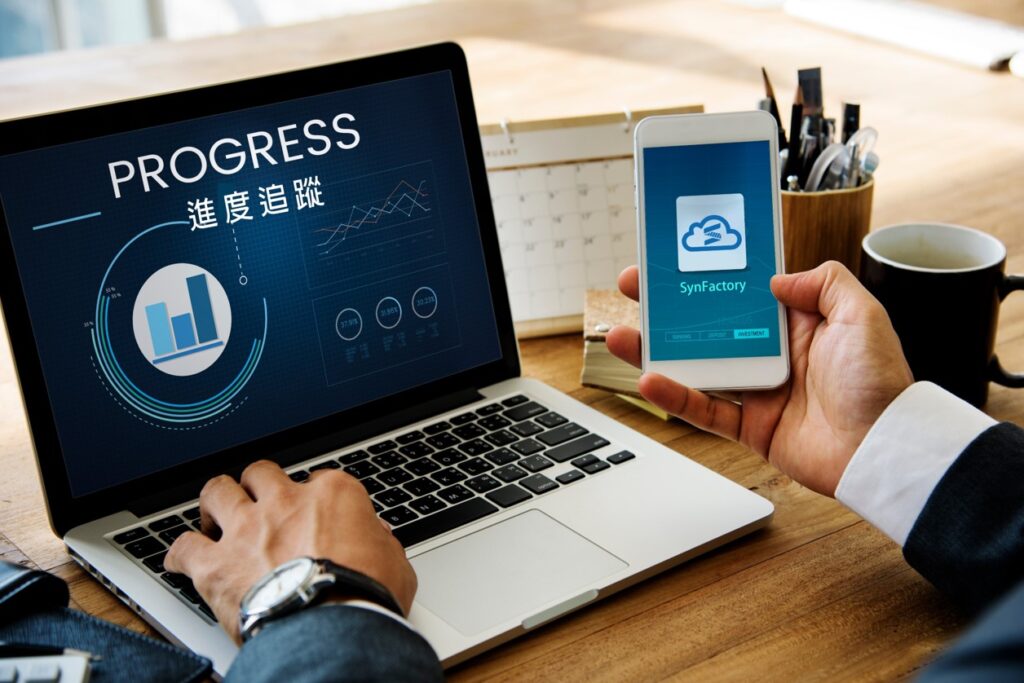
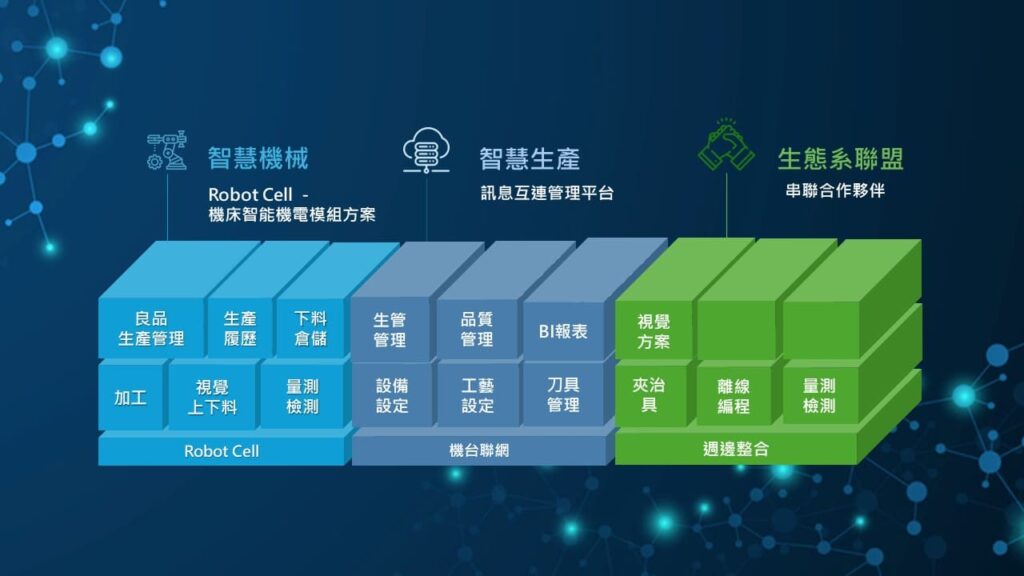
Lightweight
The modular system design allows for the selection of functional modules based on requirement, offering flexible and lightweight solutions for easily building a customized smart factory. Functional modules include equipment management, process management, production management, tool management, quality management, and inventory management, all of which help improve overall factory performance.
Integration
The equipment management module enables data collection through machine network, standardizes process data, and provides real-time feedback on work reporting. It seamlessly connects various modules from the factory floor to the cloud, making smart manufacturing simple and easy.
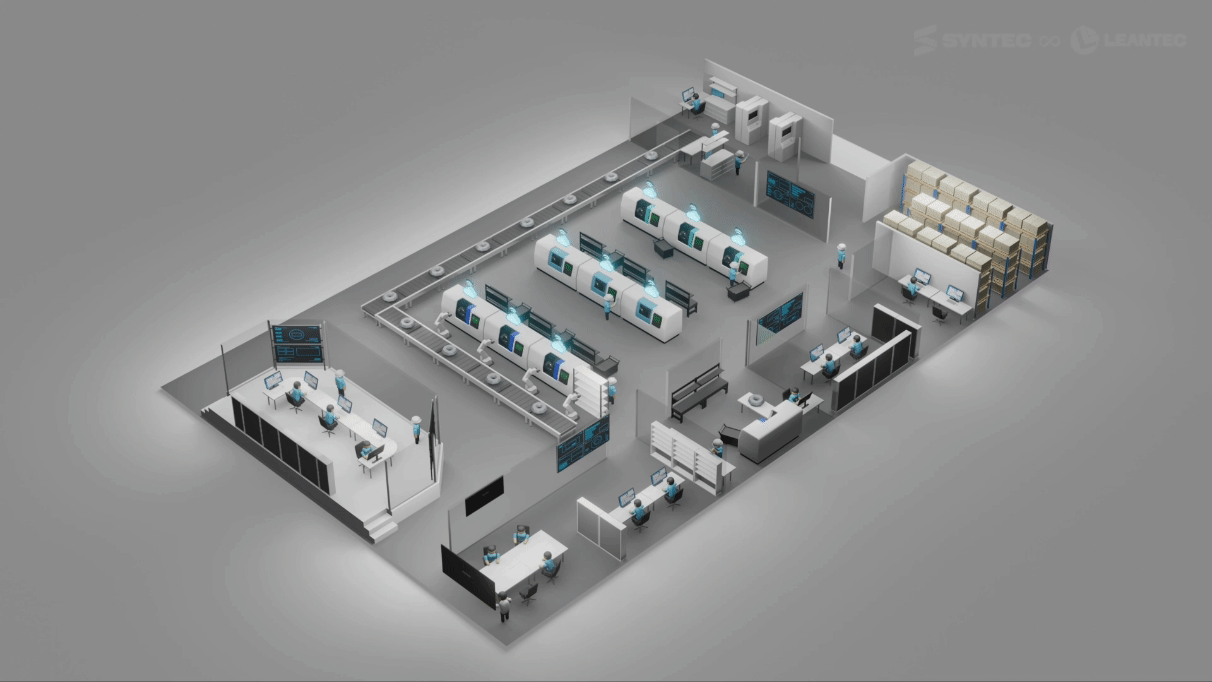
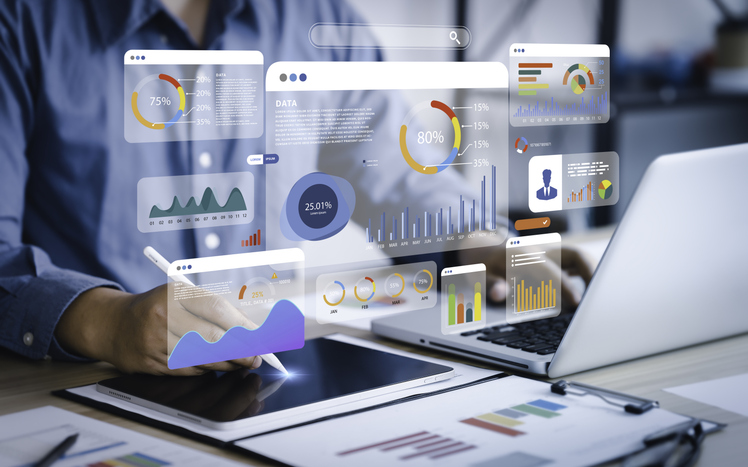
Openness
The open database enables access to key data, allowing the creation of custom dashboards, analysis reports, and more to meet factory management needs for further development. It also supports integration with existing ERP, PLM, and MES systems via APIs/ETL, eliminating the need for redundant data conversion.
Management Solutions
Phased Implementation
Machine Network Implementation
End-to-cloud integration
with data visualisatio.
Segmented Digital Transformation
Targeted solutions
with immediate effect
Achieve Smart Factory
Complete factory integration
and process optimization