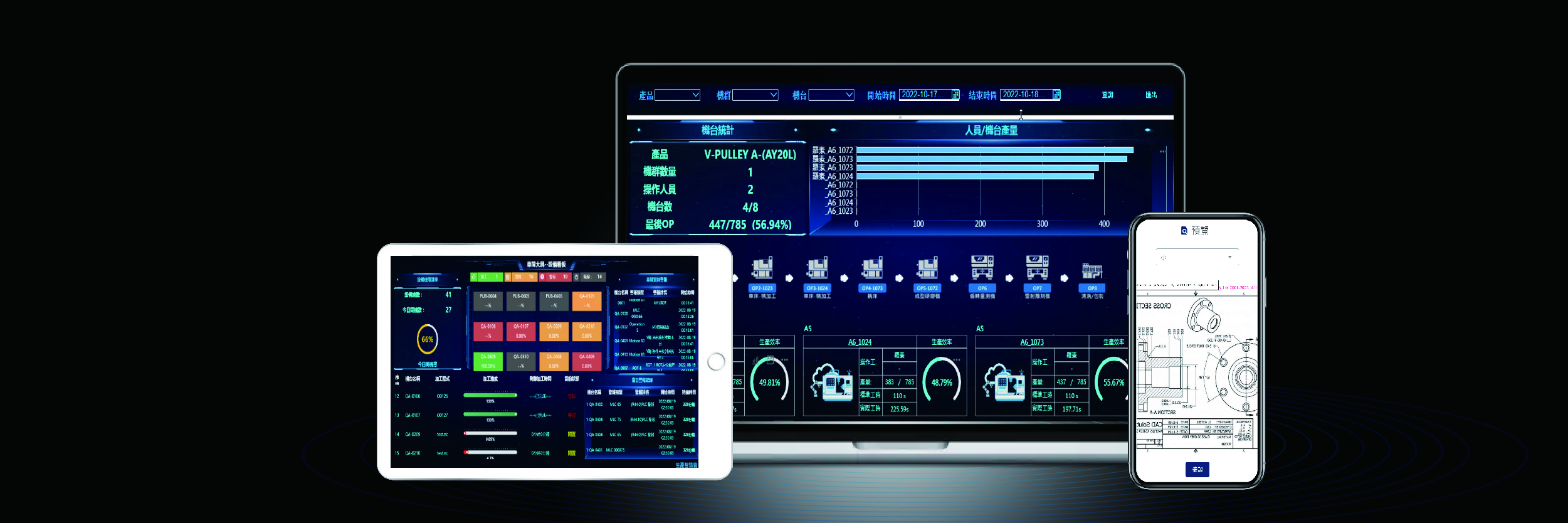
SynFactory: Smart Manufacturing Cloud
SynFactory places equipment data at the core, driving lean factory management
and serving as the “factory doctor” to diagnose and solve complex production challenges.
Designed to oversee and optimize the entire manufacturing process, SynFactory serves as the critical hub for vertical integration in smart manufacturing.
It seamlessly connects upstream with planning and management systems such as ERP, PLM, and WMS, while integrating downstream with production equipment.
By consolidating and analyzing equipment data, SynFactory dynamically issues control commands to machines based on real-time production scenarios. Simultaneously,
it collects and uploads equipment status and operational data to management systems, enabling full transparency and intelligent decision-making.
As a central pillar of smart manufacturing, SynFactory empowers factories to achieve lean production, enhance operational efficiency, and drive sustainable growth.
Benefits of the Synfactory Solution
User-Friendly
SynFactory is designed with user experience at its core, offering an intuitive and easy-to-navigate user interface (UI). Whether for first-time users or industry professionals, the system ensures a smooth learning curve and effortless operation.
Lightweight and Modular
Built on a modular and lightweight architecture, SynFactory allows users to add functional modules as needed. Unlike many traditional systems that require a large upfront investment, SynFactory enables step-by-step expansion, maximizing resource utilization while minimizing initial costs. Whether you are starting small or planning a large-scale upgrade, our solution grows flexibly with your business.
Highly Integrated
SynFactory features robust integration capabilities, connecting seamlessly with IoT devices on the shop floor and synchronizing with ERP and other existing management systems. By consolidating data across all levels onto a single platform, it greatly improves information flow and accelerates digital transformation.
Open and Extensible
With multiple connectivity options and an open data architecture, SynFactory empowers businesses to freely extract and analyze their data. This design not only unlocks deeper insights for better decision-making but also supports secondary development to meet evolving operational needs.
Management Solutions
Industrial IoT
Equipment ManagementProduct Data Management
Production Management
Quality Traceability Management
Cutting Tool
Life ManagementInventory Management
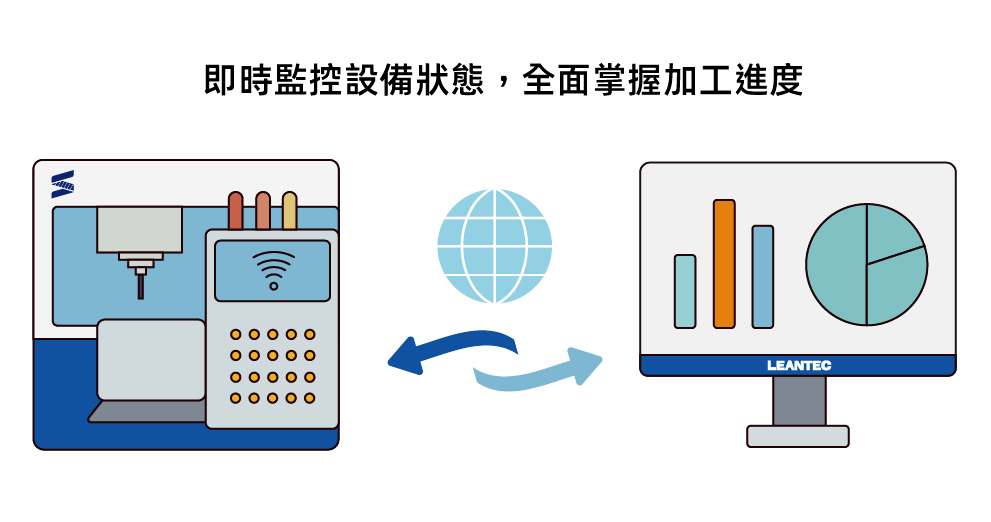
- Enhance Transparency
Deploy advanced management tools to increase on-site visibility and establish a modern IoT platform for real-time operational insight.
- Reduce Operational Costs
Automatically collect comprehensive production data, accelerate root cause analysis through lean management practices, and drive effective improvements to lower overall costs.
- High Scalability
Break through network protocol barriers across different brands of equipment. Our IIoT solutions unify diverse machines under one platform, enabling you to rapidly realize tangible benefits.
- Accelerate Smart Transformation
Enhance real-time data acquisition capabilities to overcome traditional production bottlenecks, transforming conventional manufacturing lines into high-tech smart production systems.
- Factory-Wide Energy Management
Leverage energy modeling to seamlessly translate usage data into carbon emissions, costs, and other metrics. Perform multidimensional comparisons and analyses across plant zones, machine groups, individual equipment, and personnel.
- Real-Time Equipment Monitoring
Monitor equipment power consumption in real time to quickly identify energy-intensive operations. Support your enterprise in achieving energy-saving initiatives and carbon neutrality goals.
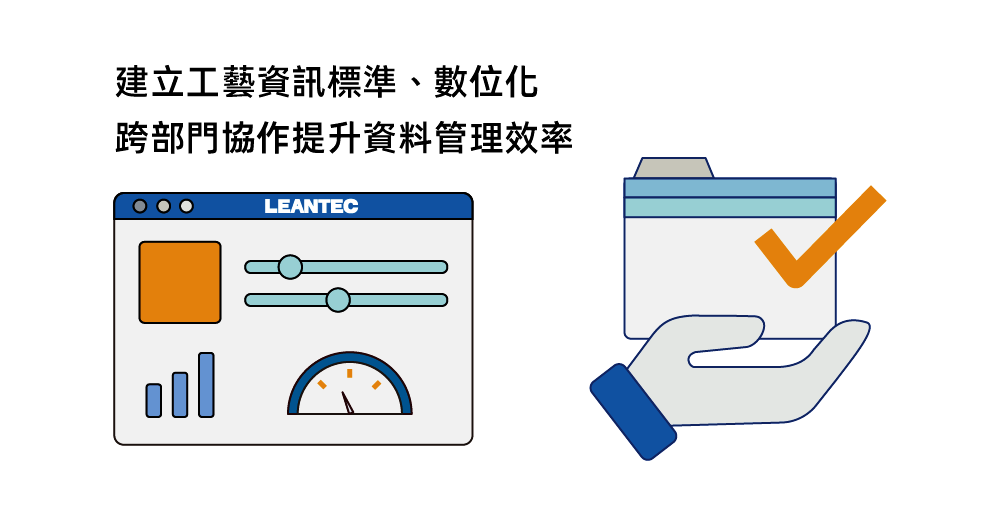
- Digitized Process Documentation
Convert product drawings, process specifications, and inspection standards from paper to digital files, significantly reducing paper usage within the factory.
- Centralized Process File Management
Store all process documents securely in the cloud, enabling centralized version control and seamless access across locations.
- Cross-Device Access to Process Data
Allow production floor personnel to quickly retrieve process information using mobile devices such as smartphones and tablets, improving operational efficiency.
- Remote File Dispatch
Deliver process files to production sites without geographic limitations, ensuring timely and accurate document distribution.
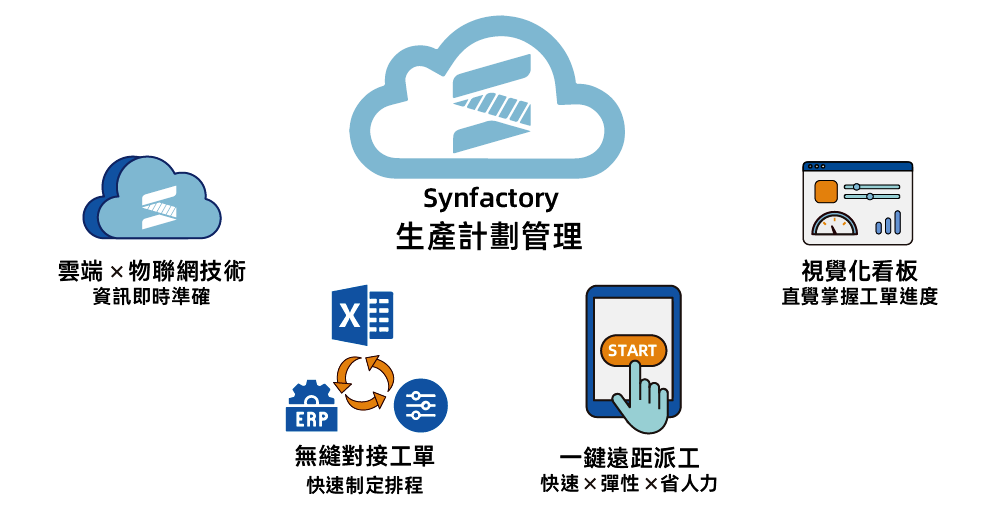
- Real-Time Shop Floor Reporting
Enable production reporting via multiple devices—including computers and smartphones—removing hardware barriers and allowing instant access to process information.
- Automated Job Dispatching
Assign production tasks to equipment with one click, eliminating the need for manual USB file transfers and minimizing transmission errors.
- Production Scheduling
Visualize and flexibly adjust production schedules through integrated work order and equipment scheduling previews, streamlining operational planning.
- Work Order Tracking
Track production progress starting from customer order delivery dates, ensuring on-time shipments and strengthening delivery reliability.
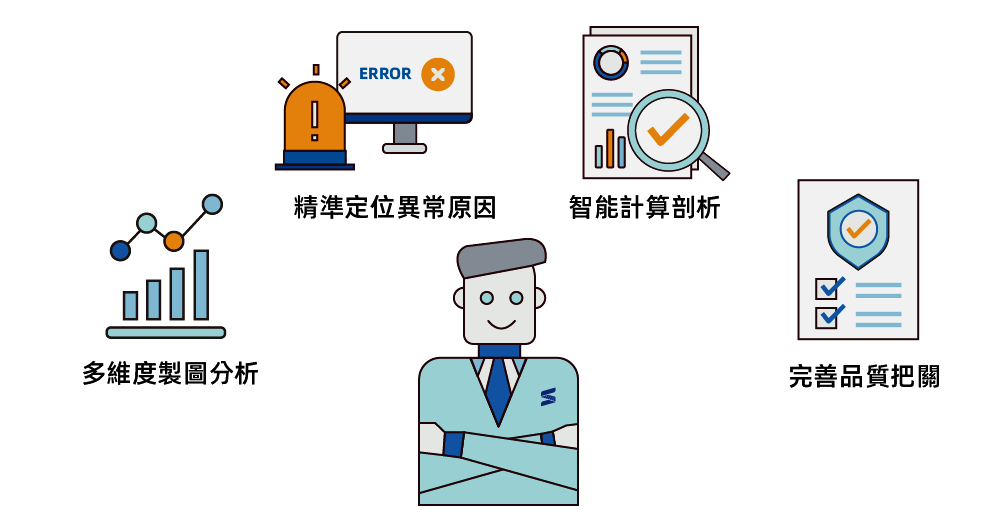
- Instant Anomaly Detection
Automatically compare measurement values against standard specifications. The system intelligently flags anomalies and digitally archives relevant data for easy retrieval.
- Instrument Integration
Seamlessly connect with calipers and advanced metrology equipment to generate comprehensive SPC (Statistical Process Control) inspection reports.
- Tool Compensation Integration
For the metal processing industry, SynFactory offers integrated remote tool compensation linked with quality management, delivering customized process control.
- Quality Traceability
Capture and store inspection data from raw material input to finished products, enabling rapid search of product quality records and generating real-time quality dashboards throughout the manufacturing process.
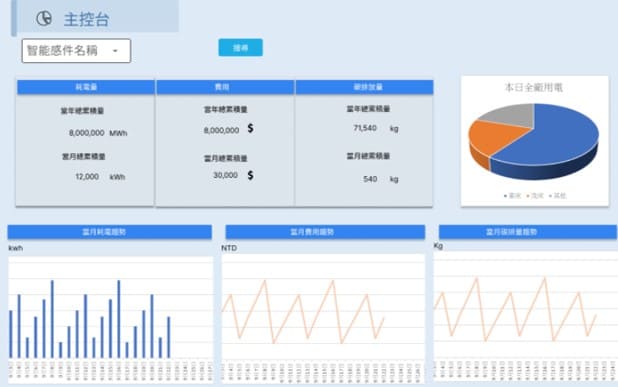
- 整廠能耗管理
通過能耗模型,直觀的轉換數據至碳排放、金額、從廠區、機群、設備、人員等各維度進行數據比對與分析。
- 設備即時監控
即時設備用電數據監控,輕易地找出用電怪獸,協助企業節能改善目標,達成減碳淨零。
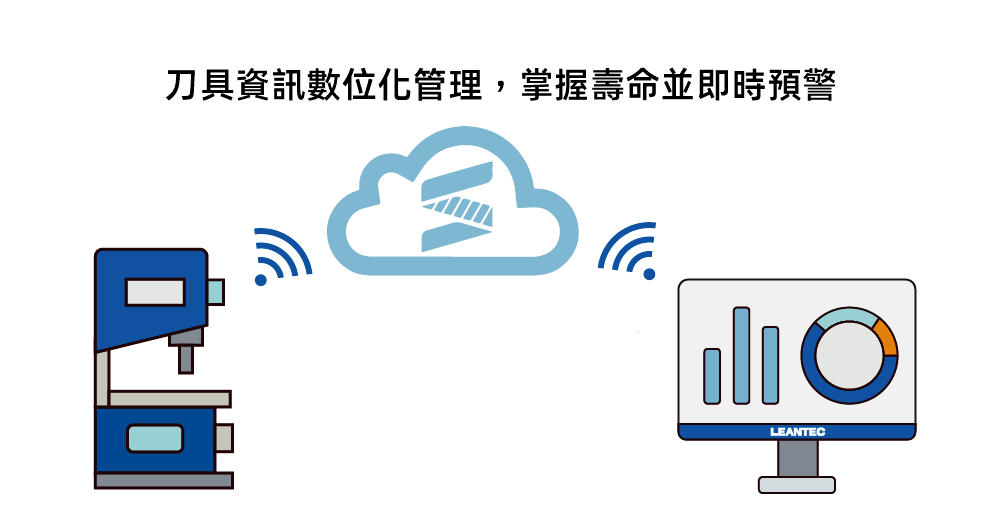
- 壽命預警
壽命值比對規範最大值,系統智慧化提示壽命預警,持續收斂刀具壽命最大值,數位留存便於後續調用。
- 歷程記錄
提供追溯紀錄,紀錄換刀的人事時地物,作為優化、分析以及管理之方向依據。
- 集中管理
解決單機版刀具壽命管理痛點,全廠不同品牌設備刀具壽命可視化,準確掌握各設備刀具使用狀態。
- 降低成本
配合 SPC 分析看板,提供更精確的壽命參考值,充分發揮刀具性能,降低刀具成本。
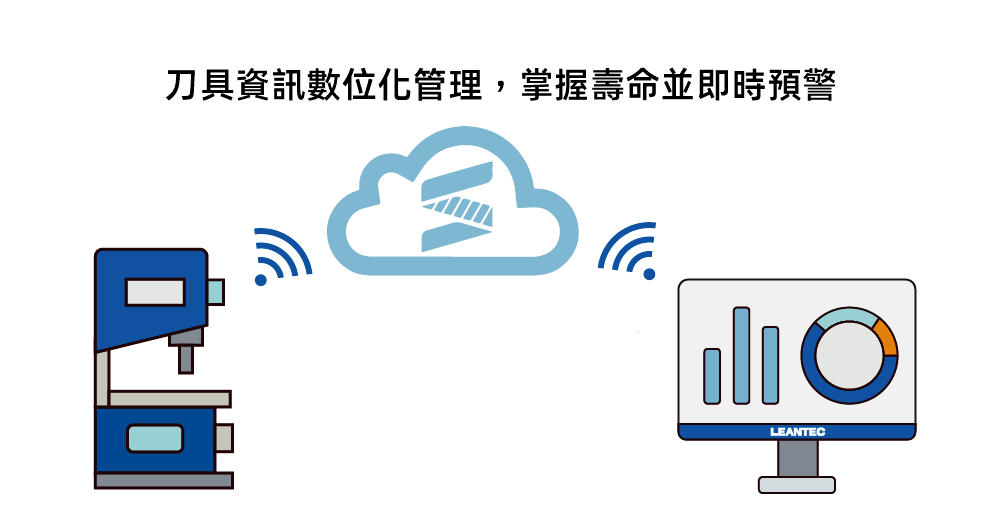
- Cutting Tool Lifetime Alerts
Automatically compare tool usage against predefined maximum thresholds. The system intelligently issues lifetime warnings, continuously refining tool lifespan estimates and digitally archiving data for future reference.
- Historical Tracking
Record detailed tool change histories, including personnel, time, and location, providing a solid foundation for optimization, analysis, and management improvements.
- Centralized Management
Resolve the limitations of standalone cutting tool life management systems. Achieve full visualization of tool usage across different brands of equipment, enabling precise monitoring of cutting tool conditions throughout the plant.
- Cost Reduction
Leverage SPC analysis dashboards to provide accurate cutting tool life reference values, maximizing tool performance and significantly reducing tooling costs.
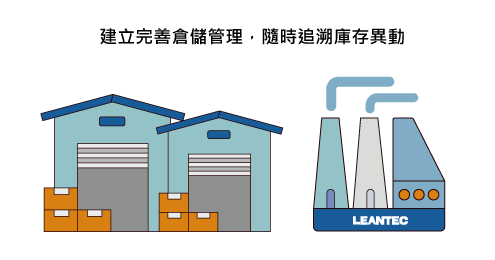
- Inventory Overview
Real-time inventory visibility with expandable secondary tables detailing material distribution across warehouses. Supports seamless inventory transfers between any warehouses with automatic generation of inbound and outbound documents. All transaction histories are traceable and reversible, allowing immediate correction of any discrepancies.
- Inventory Display
Continuously updates the availability status of all materials, with safety stock level alerts. Enables multi-dimensional inventory queries and one-click Excel exports. Expandable tables provide detailed breakdowns of materials by warehouse and storage location for easy material tracking.
- Inventory Transaction Records
Tracks every stock-in, stock-out, and transfer transaction for full traceability during inventory audits. All records are reversible—adjust incorrect transactions easily without additional stock operations, ensuring real-time inventory accuracy.
- Inventory Transfers
Simplify transfers across multiple warehouses without redundant stock-in/out operations. Users can freely select source and destination warehouses, and the system automatically generates corresponding outbound and inbound records, streamlining the transfer process.
Would you like assistance in selecting the most suitable product?
Let us know what you need — we’ll connect you with a specialist right away.